Industry Insights
Avoid costly mistakes by managing your barrel inventory using a bar code system
December 11, 2017
Barrel management systems (BMS) including tracking, maintenance and history have traditionally been adjunct functionality to many winery management systems. Perhaps simple systems are overwhelmed by the added complexity of mobile vessels versus larger tanks that usually live in one location. It’s no wonder then that many of us still track barrels via spreadsheets, clipboards and placards at row ends.
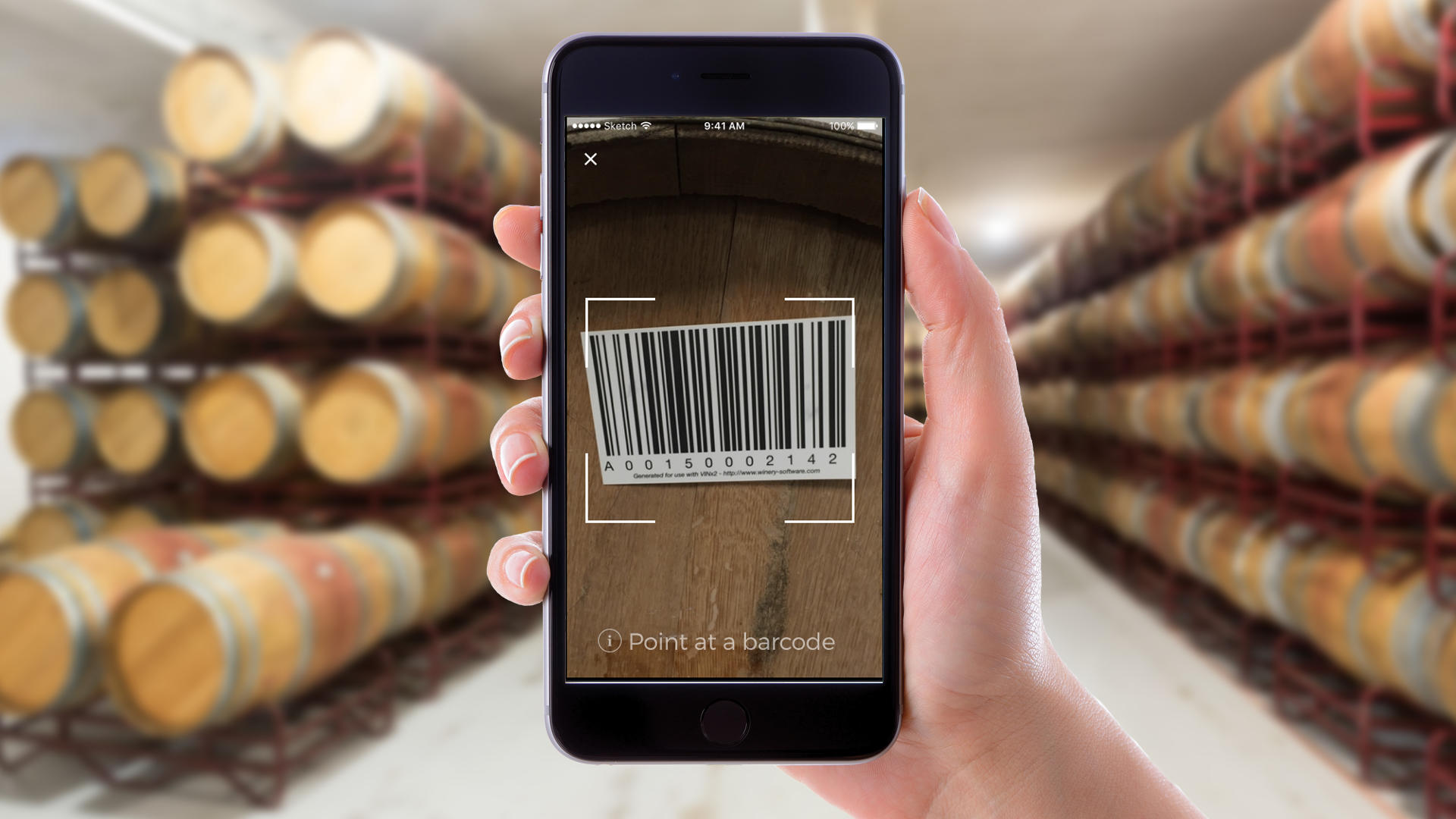
Barrels can be difficult to track and mistakes are costly
I’ve worked with many popular integrated systems that were terrible at managing barrel groups, breaking apart barrel groups, specifying which barrels got topped with what and how much KMBS to add to each barrel. Those systems couldn’t handle different size/capacity of barrels or other breakdown vessels, let alone keeping track of where they were moved to in the cellar. I’ve personally seen all this complexity lead to costly mistakes including:
incorrect blends
white juice into previously red barrels
maintenance additions out of proportion with allowable amounts, i.e. damaged wines
lost barrels
Purpose built scanners versus iPhone, iPad and Android devices
The better systems include the ability to work with a bar code scanner for ultimate efficiency, less opportunity for errors, and ease of input for individual vessel tracking. Bar code scanning can be done by a purpose built device, much like those you see at grocery stores and Costco. Other systems allow users to scan with their personal mobile devices, like iPhone, iPad and Android devices, etc. The purpose built scanners utilized are generally rugged, moisture resistant and can focus a laser beam scanner up to barrels stacked six high. Smartphones and tablets can’t be relied on to perform as ruggedly or from such distances, but their constant presence in the cellar is undeniable. Ideally having the flexibility to work with both kinds of devices will fit just about any workplace.
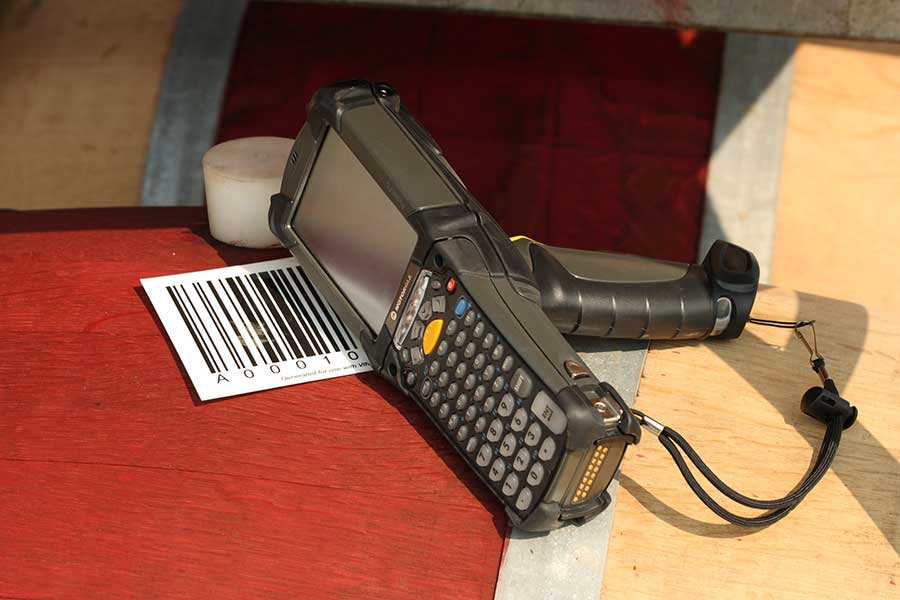
My experience suggests that rugged purpose built (read expensive) bar code scanners, usually present a return on investment (ROI) at 1,500 or more barrels, ie larger operations. Otherwise the flexibility of smartphones is paramount in any system but especially for small to mid sized operations. Having the flexibility in a system as you grow or expand is a huge benefit.
Choosing the right type of label and size
The larger the bar code, the further away you can scan it. If you have small bar codes your crew will need to get really close in order to scan that barrel as part of any cellar work. In my experience there is a trade off between bar code size and aesthetics within the barrel hall that many businesses need to manage. A common label size is approximately 2 x 4 inches in size (50mm x 100mm) but you can print smaller ones for the rings.
I recommend putting a primary and secondary label on each barrel. The primary bar code is more like a VIN number that is more permanent, should be placed on the head and have a larger bar code. The secondary label should be in a different position, on the crown ring at the two and four o-clock placement for ease of scanning from both below and at eye level.
You want your labels to be robust and to stay on during routine filling, emptying and cleaning. I recommend a high-tac adhesive label stock that’s chemical resistant and made from polyester. High-tac adhesive is key so they don’t come off after the first wash. I also recommend staying away from thermal labels such as those printed by Dymo or Brother printers as can either fade or if placed on the ring, turn black in the sun! Instead consider the Zebra series of printers.
What about RFID?
I’m often asked about the possibility of RFID as an alternative to bar coding barrels and in my experience being able to scan a barrel from a distance and using line of sight rather than waving an RFID wand past the barrel is much more efficient and costs less to maintain. You also get the flexibility to add more information to your labels. RFID is generally not compatible with out-of-the box smartphones either and so you get the added advantage of lower hardware costs.
How does vintrace stack up?
vintrace has once again set the bar in our industry by offering all the capabilities as well as including being the first to offer a free App for both iOS and Android personal devices. The best thing about the App is the functionality included is part of the base module of vintrace. For larger operations, you can purchase the rugged scanners which work on WIFI or have the capability to work offline and sync back to vintrace at a later date. This is particularly useful in a barrel cave with no signal. vintrace also incorporates bar code scanning for more common winery operations, including; work orders, labs, harvest scheduling, tank and stock bar code tagging.
Check your system against vintrace to see how it stacks up to these features:
No more double entry, scan the work order and then the barrels for the job
Scan barrels to easily update their location
Check the latest composition and analysis all from the handheld device
Compatible with a range of robust Motorola scanners
Barrels can still be scanned when outside of wireless range
Prevent lost barrels and other costly cellar mistakes
Print your own robust and cost effective Zebra bar code labels
A little about me
After a successful career in corporate America, I transitioned to the wine industry and have become an industry veteran with 10+ years experience as a grower, winemaker, and winery General Manager.
My role as former General Manager for Carneros Vintners custom crush facility and sister facility Lodi Vintners, was the impetus for my investigation of winery production software options. My work with a variety of wineries exposed me to an array of winery software before deciding on the vintrace platform to run the custom crush facilities and since, a few small and larger boutique wineries. My hands on winery experience and real life use of vintrace are the foundation of my success representing the vintrace software platform in North America.